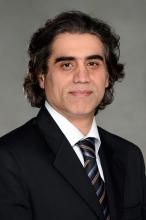
Ahmad Barari
PhD
Professor
Mechanical and Manufacturing EngineeringIntegrating data in the design, manufacturing and inspection of products across a digital platform.
Areas of expertise
- PhD in Mechanical Engineering University of Western Ontario 2006
- MSc in Mechanical Engineering Sharif University of Technology 1997
- BSc in Mechanical Engineering Amirkabir University of Technology 1995
Workshop Chair
University of Technology of Troyes, France June 30, 20168th IFAC Conference on Manufacturing, Modelling, Management & Control
A Review on Geometric Tolerances and Surface Integrity in Additive Manufacturing Products
University of Guilan, Guilan, Iran April 29, 2016Invited Lecture, Faculty of Engineering
Workshop on Additive Manufacturing Additive Manufacturing and 3D Printing
Ottawa, Ontario May 11, 201515th IFAC Symposium on Information Control in Manufacturing (INCOM 2015)
Analysis of Nonlinear Oscillation of Circular Curved Carbon Nanotube
Beijing, China August 5, 2013The 13th IEEE International Conference on Nanotechnology
Analytical Solution for Nonlinear Vibration of Sinusoidal Curved Carbon Nanotube
Montreal, Quebec July 23, 20134th Canadian Conference on Nonlinear Solid Mechanics (CanCNSM2013)
Comparing the Uncertainty of Coordinate Metrology as a Function of Sampling Strategy in Optical and Tactile Inspection Systems
San Diego, California July 22, 2013The 29th Coordinate Metrology Systems Conference (CMSC)
Minimizing Bone Removal Based on Humeral Implant Alignment in Total Elbow Arthroplasty
University of Bergamo, Bergamo, Italy June 17, 2013International CAD Conference, CAD'13
Substituting Simple Structural Beam-Frame Substructures with Equivalent Beam-Plate Combinations
University of Bergamo, Bergamo, Italy June 17, 2013International CAD Conference, CAD'13
Measurement
2016-05-14
Evaluation of the tolerance zone using discrete measured points plays a critical role in today’s metrology and industrial applications. The deviation zone is typically evaluated using a fitting method that fits an ideal desired geometry to locate measured points while a function of the Euclidean distances of the measured points to the ideal surface becomes minimum. This paper presents a quick and reliable algorithm called Dynamic Principle Component Alignment (DPCA) for fitting complex surfaces to the coordinate metrology sample points using the information that is dynamically generated by Principal Component Analysis (PCA) of the measurement data and the corresponding fitted geometry.
Journal of Applied Mechanical Engineering
2015-12-12
This paper presents a new application framework for aerodynamics-based shape optimization of passenger cars. The rear geometry of a passenger car is the focus of this study due to its significant influence on the aerodynamic characteristics of vehicles.
Acta IMEKO
2015-12-01
In order to comprehend an entire surface's deviation zone, infinite measured points are required. Using the common measurement techniques through coordinate metrology, a limited number of surface actual points can be acquired. However, the obtained points would not provide sufficient information to examine the geometry thoroughly. A novel approach to predict surface behaviour via Distribution of Geometric Deviations (DGD) is examined in this paper.
Journal of Sound and Vibration
2015-09-29
A novel procedure for the nonlinear vibration analysis of a curved beam is presented. The Non-Uniform Rational B-Spline (NURBS) is combined with the Euler−Bernoulli beam theory to define the curvature of the structure. The governing equation of motion and the general frequency formula, using the NURBS variables, is applicable for any type of curvatures, is developed.
Rapid Prototyping Journal
2015-10-01
This paper aims to propose a global adaptive direct slicing technique of Non-Uniform Rational B-Spline (NURBS)-based sculptured surface for rapid prototyping where the NURBS representation is directly extracted from the computer-aided design (CAD) model.
IFAC-PapersOnLine
2015-09-01
Surface integrity is a crucial issue that needs to be improved in the additive manufactured products. Precise evaluation of surface integrity demands a detailed understanding of the surface behaviour. Optical surface and roughness measurement sensors only provide information on the discrete points measured from the manufactured surface without the details of the surface topography. Throughout this paper, a methodology is developed to approximate the surface behaviour.
IFAC-PapersOnLine
2015-09-01
Additive manufacturing and topological optimization are two key technologies that have good symbiosis. Several issues have been solved in the area of both technologies. Additive manufacturing relaxes the design constraints related to the manufacturability of a part. A diesel engine support is topologically optimized.
IFAC-PapersOnLine
2015-09-01
Most commonly used Additive manufacturing (AM) technologies are developed based on a layered manufacturing process to fabricate 3D models. However, a critical drawback that reduces the surface quality of the AM parts is the staircase effect as a direct result of the layered deposition of the material. The final surface roughness of the products has been a key problem in AM. In this paper, a new approach to model surface roughness in Fused Deposition Modeling (FDM) is proposed.
Journal of Manufacturing Science and Engineering
2014-10-24
Inspection of surface integrity in additive manufacturing (AM) parts essentially needs a detailed understanding of their actual surface topography. Today's optical surface topography and roughness measurement sensors only provide information on the discrete points measured from the manufactured surface and not a detailed reconstruction of the surface topography. This paper presents a finite difference approach for reconstruction of the surface topography using sample measured data points.
Vehicle System Dynamics: International Journal of Vehicle Mechanics and Mobility
2014-07-10
A methodology is presented in this work that employs the active inverted wings to enhance the road holding by increasing the downward force on the tyres. In the proposed active system, the angles of attack of the vehicle's wings are adjusted by using a real-time controller to increase the road holding and hence improve the vehicle handling.
First Place Winner
2010 Ontario Centre of Excellence Connection Competition (OCE)As the Capstone Project’s Academic Advisor, Dr. Barari's student team won the 2010 OCE Connection Competition.
Second Place Winner
Formula SAE 2010 Student CompetitionAs the Formula SAE Racing Car’s Academic Advisor, Dr. Barari's student team won the 2010 Student Competition held at the University of Toronto.
Teaching Excellence Award 2009
Âé¶¹´«Ã½ University June 1, 2009Awarded for his contributions to teaching in the Faculty of Engineering & Applied Science.
Adjunct Professor
Department of Mechanical and Materials Engineering, University of Western Ontario May 1, 2010Dr. Barari collaborates on faculty research and supervises the work of graduate students.
Post Processing of Additive Manufacturing ABS Parts Using Chemical Solution $25000
NSERC Engage Grant April 1, 2015In partnership with Cimetrix Ltd., this research project aims to improve accuracy in the post-processing of 3D printing parts through Precision Addictive Manufacturing (PAM). PAM removes previous design limitations by enabling the development of hybrid materials geared to specific industry needs.
Optimization of the Curing Cycles in Selective Sintering Process $24932
NSERC Engage Grant April 1, 2015In partnership with Anubis Engineering Solutions, this one-year research project aims to optimize the manufacturing cycle by reducing the amount of costly machine time used while ensuring accuracy and quality control processes.
Integrated Platform for Coordinate Metrology to Enhance Adaptability $100000
NSERC Discovery Grant April 1, 2011This seven-year intensive research program is focused on coordinate metrology and inspection to improve quality control. Manufactured parts contain errors in their physical characteristics preventing the exact desired shape. Coordinate metrology allows for complex geometric shape deviations to be measured, then modelled, to reduce waste and ensure better process control.
Coordinate Metrology Society
American Society for Precision Engineering
Professional Engineers of Ontario
American Society of Mechanical Engineering
- Automotive Structural Design (AUTE 4060U)
This course focuses on design, analysis and manufacture of vehicle structure. Students will learn about the fundamental design aspect in different categories of vehicles and practice design procedures useful for different vehicle structures. The various manufacturing and assembly techniques used in production of the vehicle structure will be introduced. The course contents include a review of fundamental vehicle loads and their estimation, terminology and overview of vehicle structure types including Body-On-Chassis, Ladder Frame, Grillage Frame, Backbone, Monocoque, Space frame, unitary body structures, torsion and bending stiffness, Stiffness optimization, fatigue analysis, Design and analysis of body subassemblies and model variants, sizing of sections and joints, Engineering Materials and their incorporation into vehicle design, Material property charts, Material selection, Auto body design, Crashworthiness and its influence on vehicle design. - Engineering Design (ENGR1025U)
A project-based introduction to the engineering design process, computer-aided drafting, and the use of design tools and software packages for engineering design. Open-ended design-build projects by individuals and groups and written and oral technical communications. Basics of project management including organizing, planning, scheduling, controlling, and application of spreadsheets and project management software. - Concurrent Engineering and Design (MECE 2310U)
This course covers the modern integrated product development process. Unlike the traditional product development approach, concurrent (simultaneous) engineering and design reunites technical and nontechnical disciplines and brings forward a philosophy of cross-functional cooperation in order to create products which meet pre-determined objectives, and are better, less expensive, and more quickly brought to market. It is a process in which appropriate disciplines are committed to work interactively to analyze market and customer requirements in order to improve the end-to-end process by which products are conceived, designed, manufactured, assembled, sold to the customer, serviced, and finally disposed of. The concept of design is presented. Brainstorming, creativity methods, design for manufacturing, design for assembly, design for cost, and design for quality, life cycle design, reverse engineering, and rapid prototyping are addressed. Teamwork and communication skills are developed. - Fluid Power Systems (MECE 3320U)
The course reviews relevant fluid mechanics principles and proceeds with treatments of individual components. Components analyzed include: pumps, actuators, lines, valves and other related components. Discussions of individual components include: principles of operation, mathematical models, and design considerations. Analysis and design of fluid power systems used in industrial and processing equipment. Selected topics to include: positive displacement components, control devices, actuators, fluid transmission and system dynamics. - Design for Manufacturing (MANE 4110U)
This course covers the principles of design for manufacturing and production. Methodologies to enhance awareness of the manufacturing and manufacturability requirements during different stages of the design process. Use of inherent cost and benefits available in the manufacturing processes is studied. Design principles and guidelines for variety of typical manufacturing processes, assembly, disassembly and the role of design for manufacturing in concurrent engineering platform is cover. - Advanced Solid Mechanics and Stress Analysis (MECE 4210U)
Three-dimensional stress and strain analysis; strain energy methods for deflection; asymmetric and curved beams; bending, torsion and shear centers; beams on elastic foundations; thick cylinders; buckling and elastic stability; flat plates.